The future of automotive lighting will make way for significant innovation around current LED solutions. At a time when space is at a growing premium due to integration of sensor suite components and heat sinks are increasing in size, future iterations of lighting must consider novel ways to dissipate heat at a competitive cost. LNP™ KONDUIT™ compounds are a cost-effective, resourceefficient heat sink solution that can contribute to the scaling of LEDs.
Producing LED heat sinks using LNP KONDUIT compounds can help manufacturers avoid time-consuming processes otherwise required when using die cast aluminum and can potentially reduce associated costs by approximately 20%, provide weight reduction up to 30%, and decrease greenhouse gas (GHG) and energy footprints by up to 87%, while allowing for significant design freedom.
Through proper design, the performance of aluminum heatsinks can be matched by thermally conductive polymeric heatsinks. By leveraging the use of Computational Fluid Dynamics (CFD) software, the effect of design iterations on the overall thermal management can be predicted and the timelines for development can be significantly reduced. Furthermore, SABIC can provide additional design assistance, utilizing our Global Application Technology services, to drive innovation for cutting-edge LED lighting systems.
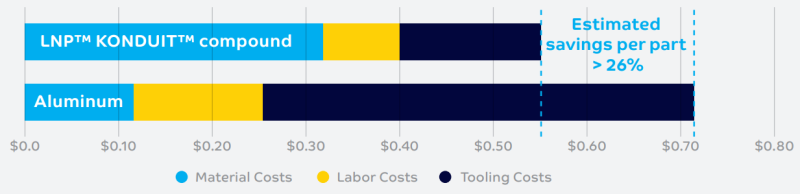
Fig1: Potential Cost Savings LNP™ Konduit™ Compound Vs Aluminum
Compliant Chemistry
LNP KONDUIT compounds comply with the RoHS Directive (2017/2102/EU), the Joint Industry Guide (JIG), the IEC ‘halogen-free’ standard (IEC 61249-2-21). LNP KONDUIT compounds do not include any of the Substances of Very High Concern as specified under the REACH Regulation (EC 1907/2006).
No Painting Needed
LNP KONDUIT compounds are available in multiple colors, which can eliminate the need for a separate painting process otherwise required for die cast aluminum.